Agas Project Manager Apply
Description:
This is a direct hire role. Suppliers will be eligible for a 15% placement fee.
Position Title: Plant Manager
Pay Rate: XX130,000-150,000/year + bonus.
Esti mated Start Date: 1/13/2025
Assignment Length: indefi nite
Est Hours Per Week: 40+ Work Schedule + Time Zone: M-F, Flexible, East Coast
Assignment Address: 2505 Shepler Church Ave SW, Canton, OH 44706 Remote or Onsight? On-site
Job Descripti on:
Job Title: Plant Manager Reports to: Zone Director, Production The ideal candidate will have:
1. Strong passion for fostering an environment of Diversity, Inclusion and Respect. 2. Experience with developing, contributing, and supporting Airgas' commitment to a World Class Service, exceeding customer expectations and building brand loyalty.
Job Responsibilities/Accountabilities:
Operates and maintains the company's facility safely and reliably by complying with regulatory requirements, developing and leading personnel, managing costs effectively, and developing personal skills and competencies.
Medium sized facilities generally include 4-8 people at a single location.
Complies with Regulatory Requirements:
Operates the facility in compliance with all local and federal governmental regulations (FDA, OSHA, EPA, DOT, cGMP, etc) and company policies
Maintains and complies with all necessary licenses and permits.
Provides all regulatory training and maintains documentation.
Reports and investigates all incidents and ensures corrective actions are complete.
Ensures that all performance evaluations, hiring, promotions and assignments are free of any form of discrimination (EEOC)
Keeps plant hazard analysis current and displays thorough knowledge of possible hazards and associated safeguards.
Adheres to the Management of Change procedure.
Operates the Plant Safely and Reliably:
Fully supports, accurately completes, and maintains all company Health, Safety, and Environmental policies, procedures, and documentation as required
Ultimately accountable and responsible for site safety including employees, contractors, visitors and neighbors. Meets or exceeds company safety standards. Demonstrates strong safety leadership and commitment.
Implements and maintains the training matrix and Airgas U training for the site.
Owns Key Operating Documents. Maintains updated red-lines at all times. Displays detailed understanding of content and significance of each document.
Makes plant and process decisions and performs process troubleshooting. Establishes clear delegation of this authority to trained subordinates.
Fosters positive customer and intercompany department relationships.
Delivers the quality and quantity of products required by the business.
Execute predictive and preventive maintenance to eliminate catastrophic failures and unplanned maintenance.
Develops annual maintenance plans and turn-around planning as needed.
Sets and maintains high housekeeping standards to exemplify and improve the company image
Develops and Leads People
Models exemplary safety behavior, leads by personal example.
Works to achieve Zero Accidents by taking a leadership role in safety.
Implements and insures compliance to Qualification and Training program for Production Technician
Conducts an annual performance review with each employee.
Implements individual development plans annually and rovides training and coaching to improve performance.
Provides candid constructive input to management decisions and actively supports those decisions.
Insists on adherence to administrative and operational policies and procedures.
Manages Costs:
Understands, monitors and optimizes operating costs within authorized budget.
Identifies and implements opportunities to reduce costs within delegated authorization. Participates in the Capital Planning Process and the Yearly Expense Budgeting Process Controls overtime within established limits.
Continuously improves efficiency and availability indicators.
Utilizes national purchasing agreements and frame agreements.
Skill Set/Knowledge/Expertise:
Technical and working understanding of the Air Separation or Carbon Dioxide liquefaction plant process or applicable process plant industry experience
Familiarity with regulatory requirements for operating plants, including Process Safety Management, OSHA regulations, EPA regulations, EEOC guidelines, FDA regulations (where applicable), state and local requirements.
Strong computer and business application skills
Trainable on Distributed Process Control (DCS) or PLC operation and troubleshooting.
Able to deliver and explain training material to operating personnel.
Extremely organized and effective at time management able to establish and maintain a plant filing system and control of engineering documents. Ability to read and red-line key operating documents.
Displays mechanical and electrical aptitude for equipment operation and troubleshooting.
Working knowledge of commercial agreements and AL customer relations.
Excellent communication and team leadership skills.
General understanding of accounting principles and working knowledge of plant operating budgets.
Highest Level of Education Required for this Position: HS Diploma
Position Title: Plant Manager
Pay Rate: XX130,000-150,000/year + bonus.
Esti mated Start Date: 1/13/2025
Assignment Length: indefi nite
Est Hours Per Week: 40+ Work Schedule + Time Zone: M-F, Flexible, East Coast
Assignment Address: 2505 Shepler Church Ave SW, Canton, OH 44706 Remote or Onsight? On-site
Job Descripti on:
Job Title: Plant Manager Reports to: Zone Director, Production The ideal candidate will have:
1. Strong passion for fostering an environment of Diversity, Inclusion and Respect. 2. Experience with developing, contributing, and supporting Airgas' commitment to a World Class Service, exceeding customer expectations and building brand loyalty.
Job Responsibilities/Accountabilities:
Operates and maintains the company's facility safely and reliably by complying with regulatory requirements, developing and leading personnel, managing costs effectively, and developing personal skills and competencies.
Medium sized facilities generally include 4-8 people at a single location.
Complies with Regulatory Requirements:
Operates the facility in compliance with all local and federal governmental regulations (FDA, OSHA, EPA, DOT, cGMP, etc) and company policies
Maintains and complies with all necessary licenses and permits.
Provides all regulatory training and maintains documentation.
Reports and investigates all incidents and ensures corrective actions are complete.
Ensures that all performance evaluations, hiring, promotions and assignments are free of any form of discrimination (EEOC)
Keeps plant hazard analysis current and displays thorough knowledge of possible hazards and associated safeguards.
Adheres to the Management of Change procedure.
Operates the Plant Safely and Reliably:
Fully supports, accurately completes, and maintains all company Health, Safety, and Environmental policies, procedures, and documentation as required
Ultimately accountable and responsible for site safety including employees, contractors, visitors and neighbors. Meets or exceeds company safety standards. Demonstrates strong safety leadership and commitment.
Implements and maintains the training matrix and Airgas U training for the site.
Owns Key Operating Documents. Maintains updated red-lines at all times. Displays detailed understanding of content and significance of each document.
Makes plant and process decisions and performs process troubleshooting. Establishes clear delegation of this authority to trained subordinates.
Fosters positive customer and intercompany department relationships.
Delivers the quality and quantity of products required by the business.
Execute predictive and preventive maintenance to eliminate catastrophic failures and unplanned maintenance.
Develops annual maintenance plans and turn-around planning as needed.
Sets and maintains high housekeeping standards to exemplify and improve the company image
Develops and Leads People
Models exemplary safety behavior, leads by personal example.
Works to achieve Zero Accidents by taking a leadership role in safety.
Implements and insures compliance to Qualification and Training program for Production Technician
Conducts an annual performance review with each employee.
Implements individual development plans annually and rovides training and coaching to improve performance.
Provides candid constructive input to management decisions and actively supports those decisions.
Insists on adherence to administrative and operational policies and procedures.
Manages Costs:
Understands, monitors and optimizes operating costs within authorized budget.
Identifies and implements opportunities to reduce costs within delegated authorization. Participates in the Capital Planning Process and the Yearly Expense Budgeting Process Controls overtime within established limits.
Continuously improves efficiency and availability indicators.
Utilizes national purchasing agreements and frame agreements.
Skill Set/Knowledge/Expertise:
Technical and working understanding of the Air Separation or Carbon Dioxide liquefaction plant process or applicable process plant industry experience
Familiarity with regulatory requirements for operating plants, including Process Safety Management, OSHA regulations, EPA regulations, EEOC guidelines, FDA regulations (where applicable), state and local requirements.
Strong computer and business application skills
Trainable on Distributed Process Control (DCS) or PLC operation and troubleshooting.
Able to deliver and explain training material to operating personnel.
Extremely organized and effective at time management able to establish and maintain a plant filing system and control of engineering documents. Ability to read and red-line key operating documents.
Displays mechanical and electrical aptitude for equipment operation and troubleshooting.
Working knowledge of commercial agreements and AL customer relations.
Excellent communication and team leadership skills.
General understanding of accounting principles and working knowledge of plant operating budgets.
Highest Level of Education Required for this Position: HS Diploma
yes
Send Us Your Feedback
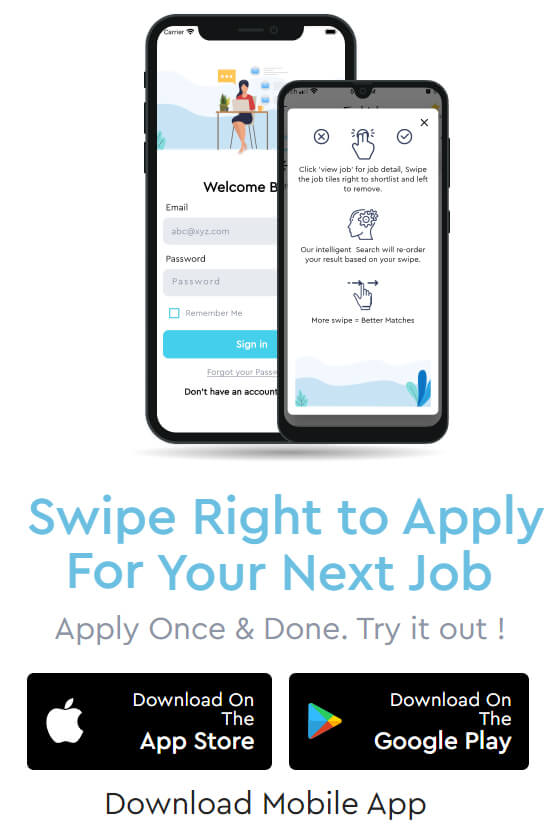
Sign In
Please check your email. We have sent you a password reset link. This link will expire in one hour.
Please input your account's email
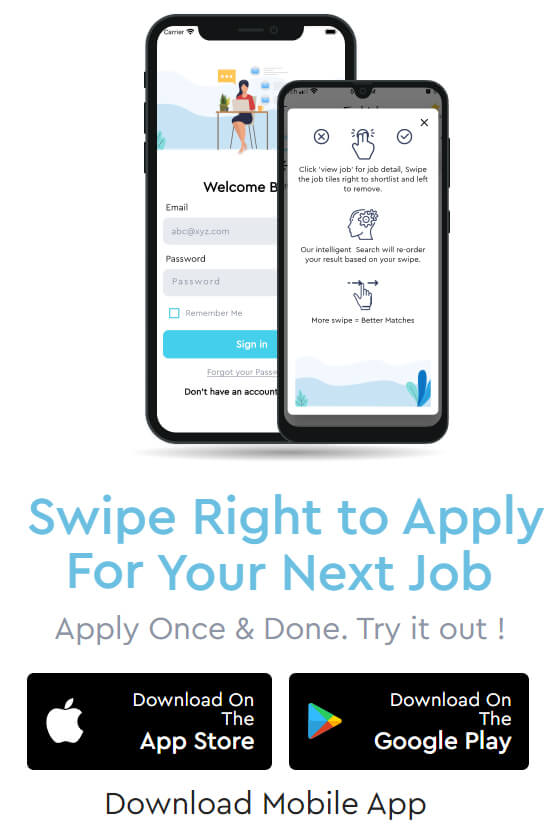
Apply to this Job
Already have account? Login here
Find Your Next Job In A Snap!
We help you find the best Jobs, Employers and Career Advice.
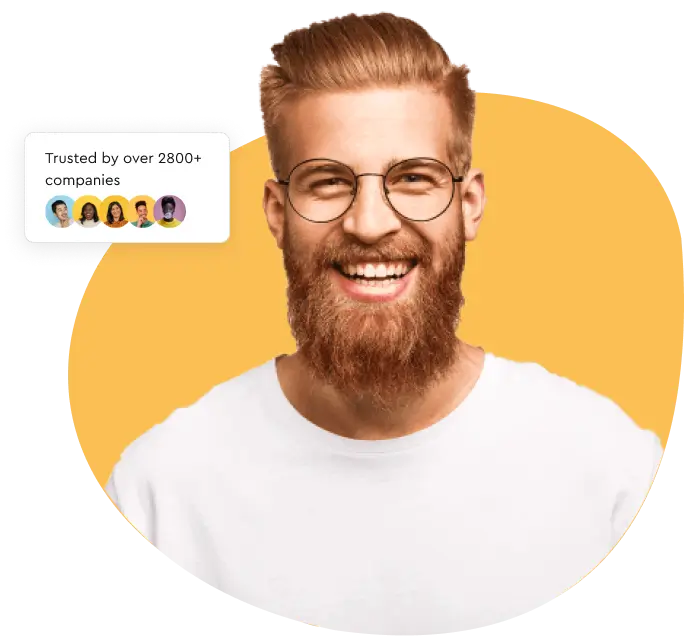
Upload your resume for a free professional assessment
Loading, Please wait..!!
Send this job to my email
Please wait..!!